METALWORKING CHEMICALS
-
Water-soluble quenching medium
-
Quenching oil
-
cutting fluid
-
Antirust agent
-
Metal cleaning agent
-
Water-glycol based fire-resistant hydraulic fluids
-
Welding anti-spatter
-
Pickling and passivation paste for stainless steel
-
Forging releasing agent
- Corrosion inhibitor /fogging inhibitor
-
Special lubricants
-
Water treatment agents

THI®F-502 water-soluble PAG quenchant
Brand: Thinking Finechembr>Model number:THI®F-502
Appearance: transparent colorless or yellowish liquid
PH:8.0-10.0
package size: 200 KG / barrel
For sample and more info, please contact us (Email: info@thinkingchem.com)
Appearance: transparent colorless or yellowish liquid
PH:8.0-10.0
package size: 200 KG / barrel
For sample and more info, please contact us (Email: info@thinkingchem.com)

This product is a non-flammable polymer quenchant, which can effectively improve the heat treatment working environment and improve the quenching quality of parts. It has inverse solubility to water. Different cooling capacities between water and oil can be obtained by adjusting temperature, concentration and stirring speed. This product is suitable for various heat treatments such as integral quenching, induction quenching, carburizing quenching, aluminum alloy solution heat treatment, etc. It can be used for heat treatments of carbon steel, alloy steel, cast iron and other workpieces.

①Adjust the concentration of quenchant to obtain different cooling rates between water and oil.
②Non-flammable, no oil fume, no fire hazard, clean production environment, eco-friendly and no pollution.
③ Effectively reduce the tendency of distortion and cracking caused by water quenching. Increase the depth of quenching layer, obtain uniform quenching hardness, and no soft spots.
④It has excellent anti-rust and anti-corrosion ability for parts, quenching tank and cooling circulation system.
⑤High shear strength. the polymer is less likely to burn-in or deteriorate, extend service life.
⑥The amount of carry-out is small, low cost and cost efficient.
②Non-flammable, no oil fume, no fire hazard, clean production environment, eco-friendly and no pollution.
③ Effectively reduce the tendency of distortion and cracking caused by water quenching. Increase the depth of quenching layer, obtain uniform quenching hardness, and no soft spots.
④It has excellent anti-rust and anti-corrosion ability for parts, quenching tank and cooling circulation system.
⑤High shear strength. the polymer is less likely to burn-in or deteriorate, extend service life.
⑥The amount of carry-out is small, low cost and cost efficient.

Subject | Indicator |
---|---|
Appearance | transparent colorless or yellowish liquid |
Density (25℃ g/cm3) | 1.080-1.180 |
PH | 8.0-10.0 |
Viscosity (40℃ stock solution, mpa.s) | ≥260 |
Antirust property | ≥5% has good antirust property |
Cloud point | 75±5 |
Condensation point | ≤-10℃ |
冷却特性数据(10%浓度、30℃液温、静置条件)
Subject | Indicator | Subject | Indicator |
---|---|---|---|
Maximum cooling speed ℃/s | ≥140 | T600(S) | 3.00±1.0 |
Maximum cooling temperature, ℃ | ≥600 | T400(S) | 4.00±1.0 |
V300(℃/S) | ≤65 | T200(S) | 9.00±1.0 |

①Suitable for integral quenching of carbon steel, alloy steel and cast iron. Different concentrations can be selected according to the carbon content, alloy composition, performance requirements and the size of the parts. Generally the concentration is between 5-20%.
②Suitable for induction heating and quenching of various workpieces.
③Suitable for solution treatment of aluminum alloy.
④ The traditional quenching process that used water quenching and oil cooling can be replaced by using our quenchant.
②Suitable for induction heating and quenching of various workpieces.
③Suitable for solution treatment of aluminum alloy.
④ The traditional quenching process that used water quenching and oil cooling can be replaced by using our quenchant.

①Determine the optical concentration of quenchant according to the material, size, shape, heat treatment equipment and process requirements of the workpiece.
Table of suitable concentration for different types of steel (reference value) | |||||
---|---|---|---|---|---|
5% | 10% | 15% | |||
30 | T7 | T7 | 40Mn2 | 40Mn2 | GCr15SiMn |
35 | T8 | T8 | GCr15 | GCr15 | 50CrVA |
45 | T10 | T10 | 65Mn | 65Mn | 50Mn2 |
45B | T12 | T12 | 60si2Mn | 60Si2Mn | 50CrMn |
50 | 40Mn | 40Mn | 40Mn2V | 40Mn2V | 50CrMnVA |
30Mn | 40Cr | 40Cr | GCr9SiMn | Gcr9SiMn | 40CrMoB |
60 | GCr9 | GCr9 | 42SiMn | 42SiMn | 38CrMoAL |
65 | 30CrMnTi | 30CrMnTi | 50Cr | 50Cr | 55SiMnVB |
30Cr | 35CrMo | 35CrMo | 40MnB | 40MnB | |
42CrMo | 42CrMo | ||||
Gcr6 | GCr6 | ||||
40CrV | 40CrV | ||||
carburizing and quenching | |||||
15 | 20Cr | 20CrMo | 20CrMnMo | 20CrMnMo | |
20 | 20CrV | 20Mn2 | 20crMnTi | 20CrMnTi | |
20CrNi | 20CrNi |
②Quenching tank and stirring system quenching tank are mainly made by iron welding and cement casting. Because the quenchant contains anti-rust agent, it is not necessary to paint. Paint can easily react with quenching agent. The quenchant is alkaline, so copper or aluminum auxiliary facilities of the quenching tank such as pumps and pipes should be avoided as far as possible to prevent corrosion. In order to better dissipate heat and prevent the growth of bacteria, it is recommended to install a stirring device with an appropriate stirring speed.
③If oil is replaced by the quenchant, the system and pipes need to be thoroughly cleaned. THIF-301 metal cleaner can be used for cleaning.
④Pour clean water to 50% of the normal liquid level, then pour the quenchant stock solution according to the concentration ratio, and then add clean water to the normal liquid level, while stirring and circulating until the solution is well mixed.
③If oil is replaced by the quenchant, the system and pipes need to be thoroughly cleaned. THIF-301 metal cleaner can be used for cleaning.
④Pour clean water to 50% of the normal liquid level, then pour the quenchant stock solution according to the concentration ratio, and then add clean water to the normal liquid level, while stirring and circulating until the solution is well mixed.

1. Concentration control
① Refractometer test
A handheld refractometer can be used to detect the concentration of the quenchant at the production site. The concentration is 2.5 times of the refractometer reading. For example, if the refractive index reading is 4, the concentration is 4×2.5=10%.
When first start using quenchant, since the contamination of the quenchant is not very serious, it is sufficient to use a refractometer for detection. However, after using the quenchant or a long time, due to the influence of the oxide scale brought in during the quenching of the workpiece and the impurities of the water itself, there will be relatively large errors in the detection of the refractometer. the characteristics of the cooling curve should be measured regularly (3-6 months) to correct the concentration of quenchant.
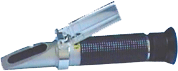
②Cooling characteristic test
The cooling characteristic tester is the most convenient and effective detecting method. The cooling characteristic tester can also be used to correct the refractive index. By detecting the low-temperature cooling rate of the quenchant (cooling rate at 300°C), the changes in the cooling performance of the quenchant can be directly monitored. If a significant change occurs, guidance and adjustment can be made immediately.
Quenchant temperature control
①In order to obtain the best cooling effect, generally the temperature of the quenchant should be controlled within the range of 10-45°C, the best quenching temperature is within the range of 20-40°C, and the highest temperature cannot exceed 55°C.
②A temperature controller can be installed at the quenching site to monitor the liquid temperature at any time.
③When designing the quenching system, the temperature of the quenchant should be taken into consideration. the circulating cooling system should be added. In lot production, the circulating cooling system should be activated.
3. Stirring control
Stirring can unify the temperature and concentration of the liquid at different positions of the quenching tank, so that different parts of the workpiece can obtain a more uniform cooling effect and can effectively improve the service life of the quenchant. Therefore, the quenching tank should have a good and effective stirring device and diversion device. Effective stirring can not only increase the quenching intensity, but also improve the uniformity of quenching effect. Stirring is important in improving the hardness and uniformity of quenching, controlling and reducing distortion, and it also plays a role of PAG quenching medium.
4. Maintenance routine of quenchant
Prevent oil stains, dust and other debris from being mixed into the quenchant and causing deterioration, stink, and further adverse effect on quenchant.
If the quenchant is in a non-use state for a long time, the quenchant should be stirred regularly (1-2 days) to prevent the growth of anaerobic bacteria and affect the effect of the quenchant. If there is bacterial growth and serious pollution, it can be treated with bactericide. The THIS-629 bactericide developed by our company is specifically aimed at the spoilage of PAG quenchant. The effect is very significant, which greatly extends the service life of the quenchant.
When intensive agitation, serious pollution, or leaks of circulation pipeline occurred, foam might be produced. If there is too much foam that affects production, you can add a defoamer.
Precipitate and filter the quenching liquid every six months to a year to keep the quenching liquid clean.
After quenching, the workpiece can be cleaned with clean water or quenching liquid. The cleaning agent can be added to the quenching tank to recycle the quenchant, which can significantly reduce the consumption of the quenchant.
When the technical requirements cannot be met by replenishing clean quenchant, it is recommended to replace the whole tank of quenchant.
If the concentration of the quenching liquid used is too low (less than 5%) or the parts have high requirements for rust resistance after quenching, an appropriate amount of antirust agent can be added to the quenching liquid separately.
① Refractometer test
A handheld refractometer can be used to detect the concentration of the quenchant at the production site. The concentration is 2.5 times of the refractometer reading. For example, if the refractive index reading is 4, the concentration is 4×2.5=10%.
When first start using quenchant, since the contamination of the quenchant is not very serious, it is sufficient to use a refractometer for detection. However, after using the quenchant or a long time, due to the influence of the oxide scale brought in during the quenching of the workpiece and the impurities of the water itself, there will be relatively large errors in the detection of the refractometer. the characteristics of the cooling curve should be measured regularly (3-6 months) to correct the concentration of quenchant.
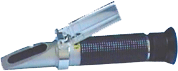
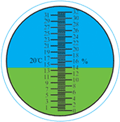
The cooling characteristic tester is the most convenient and effective detecting method. The cooling characteristic tester can also be used to correct the refractive index. By detecting the low-temperature cooling rate of the quenchant (cooling rate at 300°C), the changes in the cooling performance of the quenchant can be directly monitored. If a significant change occurs, guidance and adjustment can be made immediately.
Quenchant temperature control
①In order to obtain the best cooling effect, generally the temperature of the quenchant should be controlled within the range of 10-45°C, the best quenching temperature is within the range of 20-40°C, and the highest temperature cannot exceed 55°C.
②A temperature controller can be installed at the quenching site to monitor the liquid temperature at any time.
③When designing the quenching system, the temperature of the quenchant should be taken into consideration. the circulating cooling system should be added. In lot production, the circulating cooling system should be activated.
3. Stirring control
Stirring can unify the temperature and concentration of the liquid at different positions of the quenching tank, so that different parts of the workpiece can obtain a more uniform cooling effect and can effectively improve the service life of the quenchant. Therefore, the quenching tank should have a good and effective stirring device and diversion device. Effective stirring can not only increase the quenching intensity, but also improve the uniformity of quenching effect. Stirring is important in improving the hardness and uniformity of quenching, controlling and reducing distortion, and it also plays a role of PAG quenching medium.
4. Maintenance routine of quenchant
Prevent oil stains, dust and other debris from being mixed into the quenchant and causing deterioration, stink, and further adverse effect on quenchant.
If the quenchant is in a non-use state for a long time, the quenchant should be stirred regularly (1-2 days) to prevent the growth of anaerobic bacteria and affect the effect of the quenchant. If there is bacterial growth and serious pollution, it can be treated with bactericide. The THIS-629 bactericide developed by our company is specifically aimed at the spoilage of PAG quenchant. The effect is very significant, which greatly extends the service life of the quenchant.
When intensive agitation, serious pollution, or leaks of circulation pipeline occurred, foam might be produced. If there is too much foam that affects production, you can add a defoamer.
Precipitate and filter the quenching liquid every six months to a year to keep the quenching liquid clean.
After quenching, the workpiece can be cleaned with clean water or quenching liquid. The cleaning agent can be added to the quenching tank to recycle the quenchant, which can significantly reduce the consumption of the quenchant.
When the technical requirements cannot be met by replenishing clean quenchant, it is recommended to replace the whole tank of quenchant.
If the concentration of the quenching liquid used is too low (less than 5%) or the parts have high requirements for rust resistance after quenching, an appropriate amount of antirust agent can be added to the quenching liquid separately.

200KG/barrel packaging. Please store in cool places. The storage life is 2 years. Transported as general chemicals.



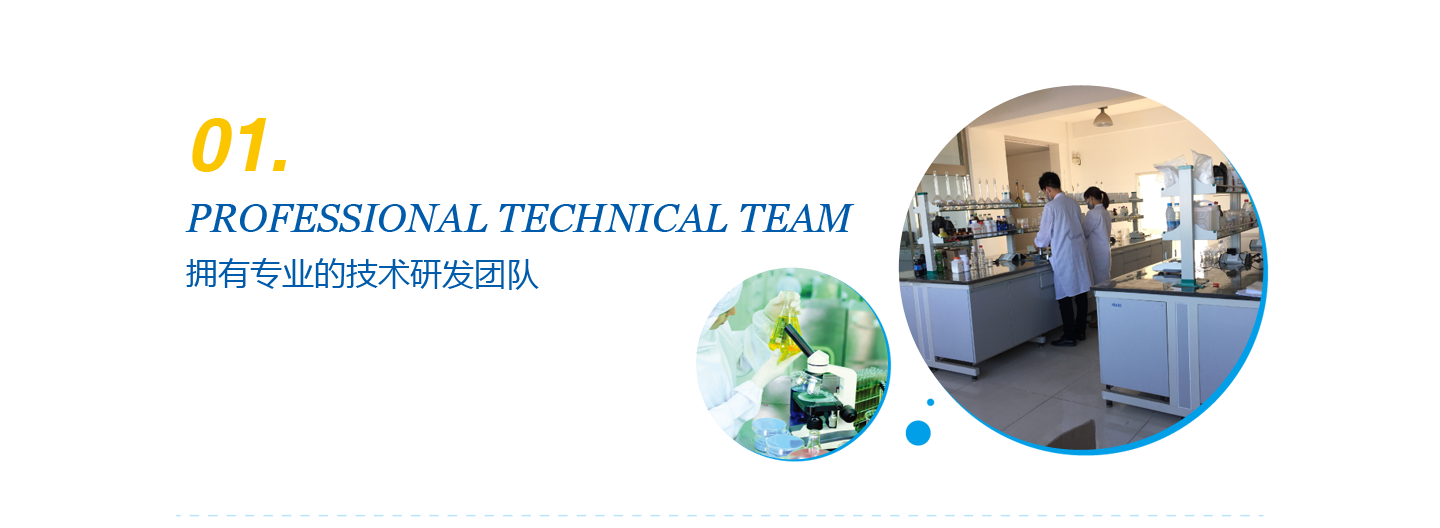
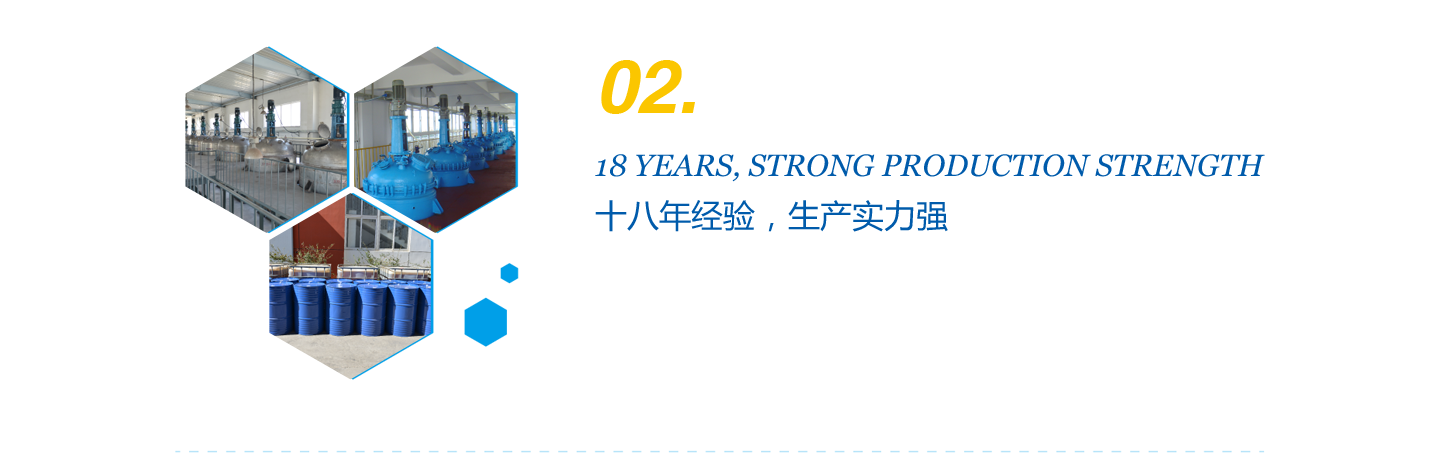
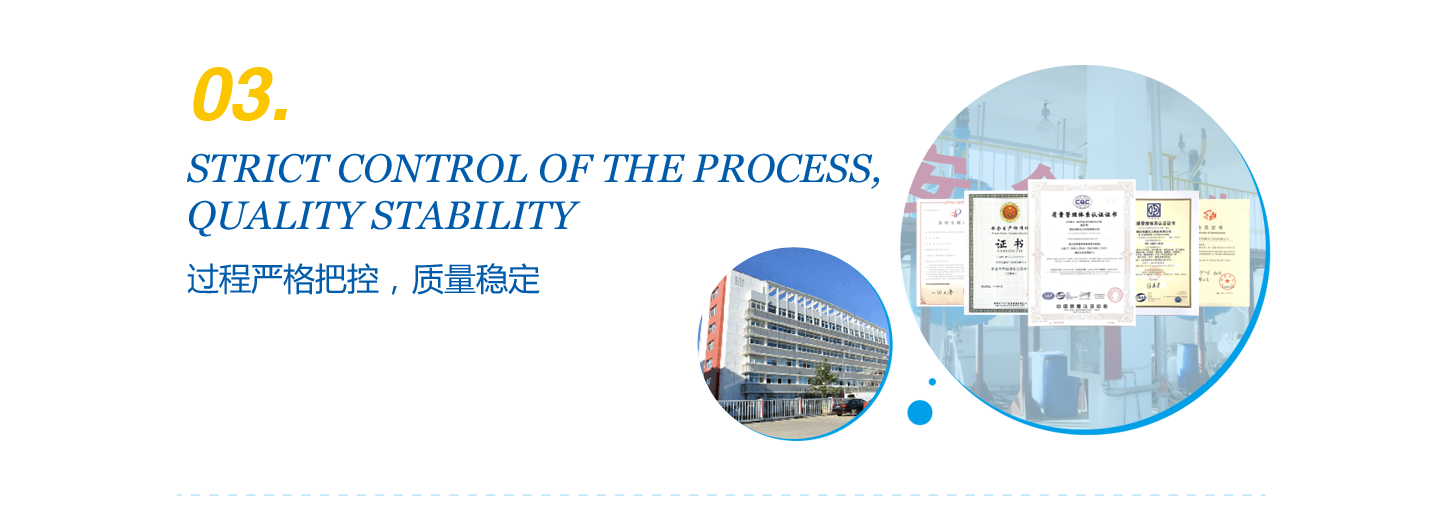
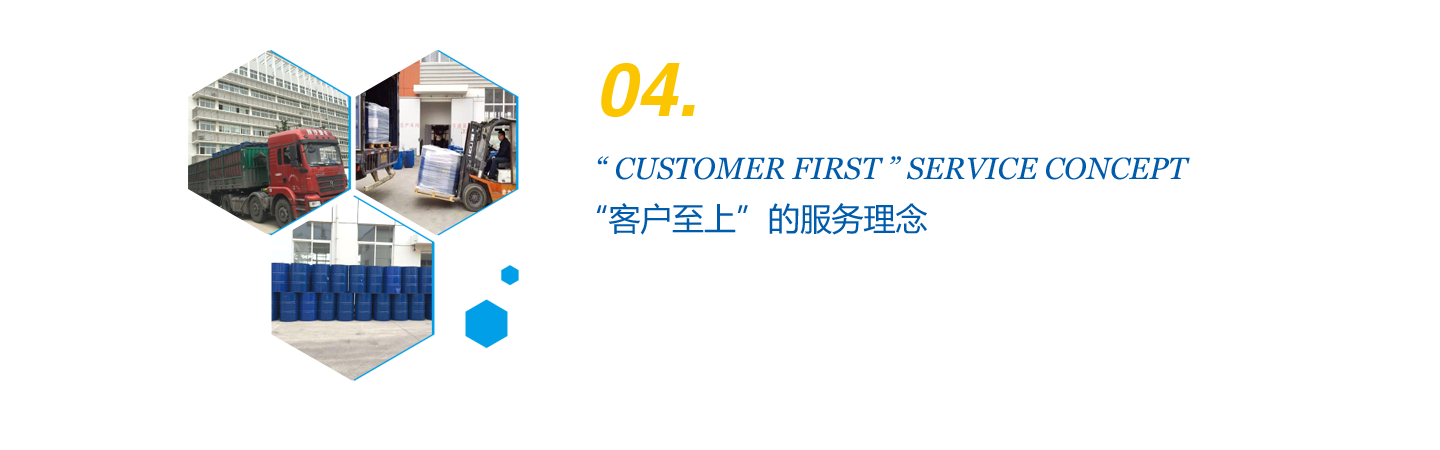
