METALWORKING CHEMICALS
-
Quenching oil
-
Water-soluble quenching medium
-
cutting fluid
-
Antirust agent
-
Metal cleaning agent
-
Water-glycol based fire-resistant hydraulic fluids
-
Welding anti-spatter
-
Pickling and passivation paste for stainless steel
-
Forging releasing agent
- Corrosion inhibitor /fogging inhibitor
-
Special lubricants
-
Water treatment agents

THI®F-518 Graded Austempering Quenching Oil
Brand: Thinking Finechem
Model number:THI®F-518
Appearance: light yellow oil
Flash point: 160-240℃
package size: 170 KG / drum
For sample and more info, please contact us (Email: info@thinkingchem.com)
Model number:THI®F-518
Appearance: light yellow oil
Flash point: 160-240℃
package size: 170 KG / drum
For sample and more info, please contact us (Email: info@thinkingchem.com)

①short steam film stage, faster cooling rate, moderate convection starting temperature, and sufficient hardening ability.
②uniform quenching hardness, small quenching distortion of the workpiece.
③the workpiece has fine luster and is easy to clean after quenching.
④Good thermal stability, long service life, and long-term stable quenching quality.
②uniform quenching hardness, small quenching distortion of the workpiece.
③the workpiece has fine luster and is easy to clean after quenching.
④Good thermal stability, long service life, and long-term stable quenching quality.

Indicator | Technical requirement | Test method | ||
---|---|---|---|---|
A | B | |||
Kinematic viscosity, 40℃,mm2/s≯ | 20 | 35 | GB/T265 | |
Flash point (open), ℃ ≮ | 220 | 240 | GB/T3536 | |
Water content, %≯ | None | None | GB/T260 | |
Pour point, ℃ ≯ | -5 | -5 | GB/T3535 | |
Corrosion (copper, 100℃,3h), degree ≯ | 1 | 1 | GB/T5096 | |
luminance, level ≯ | 1 | 1 | SH0564 | |
Thermal oxidation stability | Viscosity ratio ≯ | 1.2 | 1.2 | SH/T0219 |
Carbon Residue,% ≯ | 1.0 | 1.0 | ||
Cooling performance (liquid temperature 60℃, not stirred) | Characteristic temperature ℃ ≮ | 680 | 680 | ISO/D09950 |
Highest cooling speed ℃s ≮ | 90 | 80 |

Suitable for controllable atmosphere multi-purpose furnace, continuous furnace, mesh belt furnace, etc. Mainly used for carburizing or carbonitriding gears, clutches, thin-walled bearing rings, ring carburizing, high chromium cast iron and other types of martensite quenching.

Allowable use temperature: 80℃-140℃.
Recommended temperature: 80℃-120℃.
Recommended temperature: 80℃-120℃.

①Quenching tank: The sludge, oxide scale and carbon black should be removed from the quenching tank before use, and there must be no water in the quenching tank.
②Moisture control: Be careful not to mix in moisture. If more than 400PPM of moisture is mixed in during group quenching, it may cause uneven quenching hardness and reduce the service life of quenching oil. If there is moisture, dehydrate first.
③Control of oil temperature: use instruments to monitor and control the oil temperature to keep the oil temperature within the recommended temperature range. The quenching tank should have cooling and heating devices. When choosing a cooler, it is better to choose an air cooler. If you choose a plate heat exchanger, you must ensure that the heat exchanger does not leak (note that copper or copper alloys have an aging effect on the quenching oil and cannot be used as a radiator). On the premise of meeting the quenching requirements, try to choose a lower oil temperature to extend the service life of the quenching oil.
④String control: Propeller string is the best, followed by circulating oil pump, preferably not using air pump to stir. Set appropriate stirring force according to the material, shape and size of the workpiece.
⑤Regular cleaning of impurities: the scrap iron, oxide scale, oil sludge, oil residue and other impurities in the oil tank and circulation system should be regularly precipitated, filtered and cleaned to keep the quenching oil clean.
⑥Notice: thick and large workpieces must be quickly submerged in quenching oil. If the workpiece is half in oil and half in the air, it is likely to ignite the quenching oil and cause uneven hardening of the workpiece.
⑦ detection: regularly inspect the viscosity, flash point, water content and cooling characteristics of the quenching oil, and timely replenish the quenching oil in the oil tank.
②Moisture control: Be careful not to mix in moisture. If more than 400PPM of moisture is mixed in during group quenching, it may cause uneven quenching hardness and reduce the service life of quenching oil. If there is moisture, dehydrate first.
③Control of oil temperature: use instruments to monitor and control the oil temperature to keep the oil temperature within the recommended temperature range. The quenching tank should have cooling and heating devices. When choosing a cooler, it is better to choose an air cooler. If you choose a plate heat exchanger, you must ensure that the heat exchanger does not leak (note that copper or copper alloys have an aging effect on the quenching oil and cannot be used as a radiator). On the premise of meeting the quenching requirements, try to choose a lower oil temperature to extend the service life of the quenching oil.
④String control: Propeller string is the best, followed by circulating oil pump, preferably not using air pump to stir. Set appropriate stirring force according to the material, shape and size of the workpiece.
⑤Regular cleaning of impurities: the scrap iron, oxide scale, oil sludge, oil residue and other impurities in the oil tank and circulation system should be regularly precipitated, filtered and cleaned to keep the quenching oil clean.
⑥Notice: thick and large workpieces must be quickly submerged in quenching oil. If the workpiece is half in oil and half in the air, it is likely to ignite the quenching oil and cause uneven hardening of the workpiece.
⑦ detection: regularly inspect the viscosity, flash point, water content and cooling characteristics of the quenching oil, and timely replenish the quenching oil in the oil tank.

170KG/iron drum packaging. Please store in cool places. The storage life is 2 years. Transported as general chemicals.



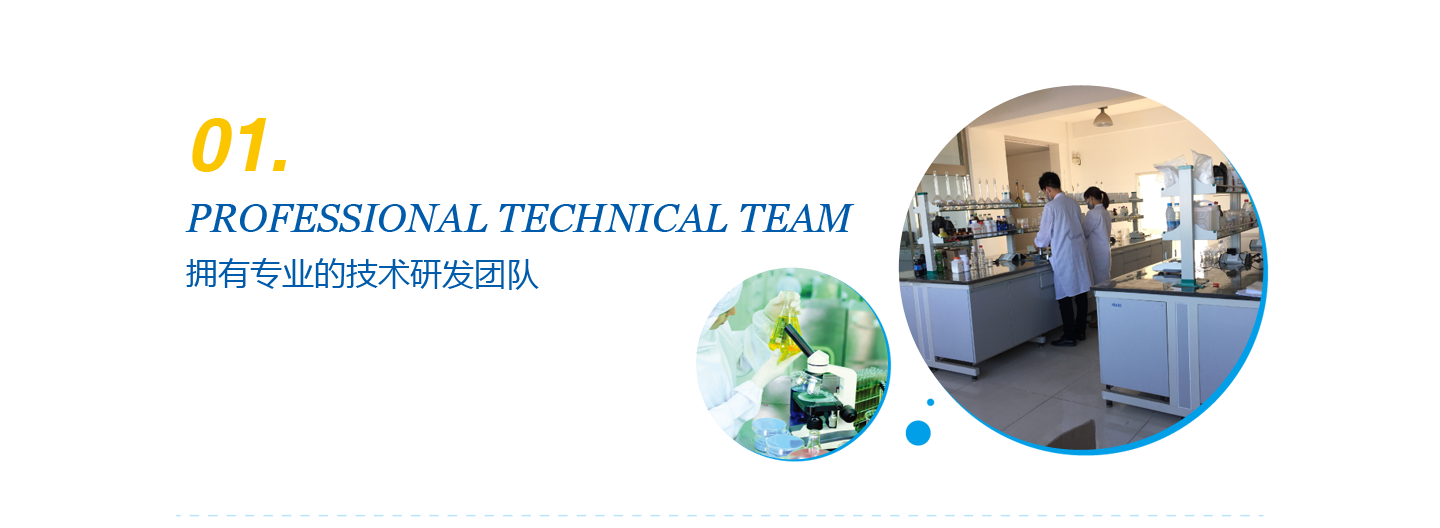
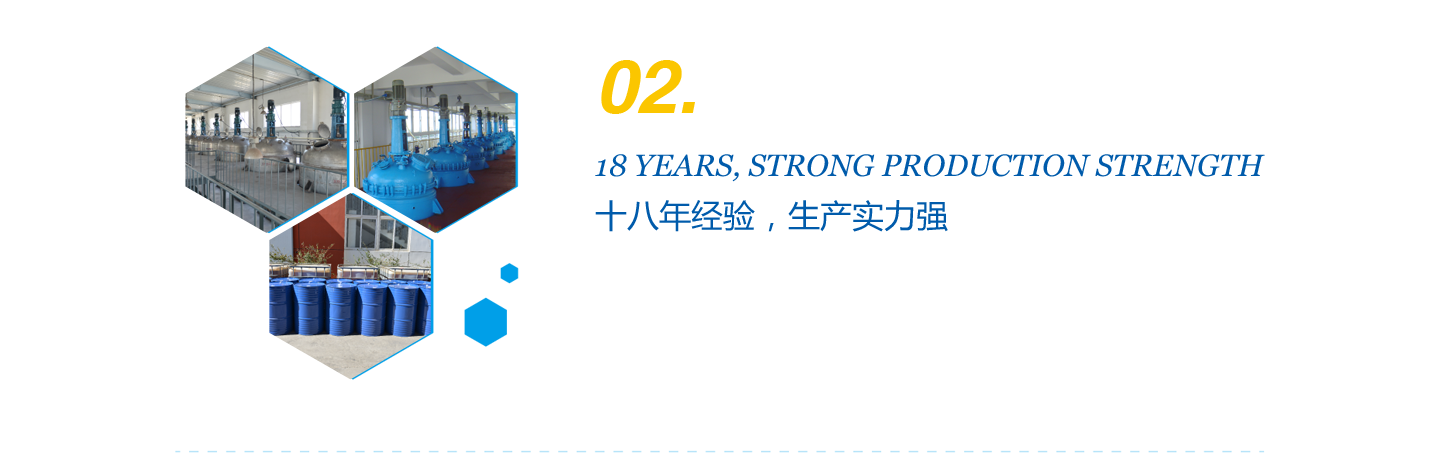
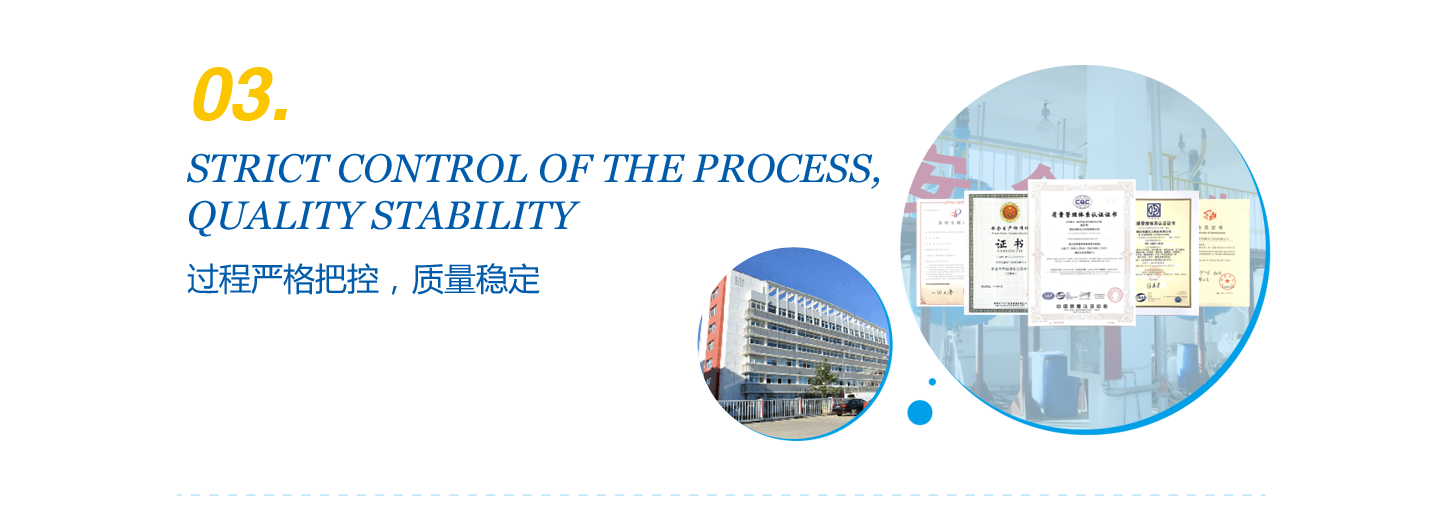
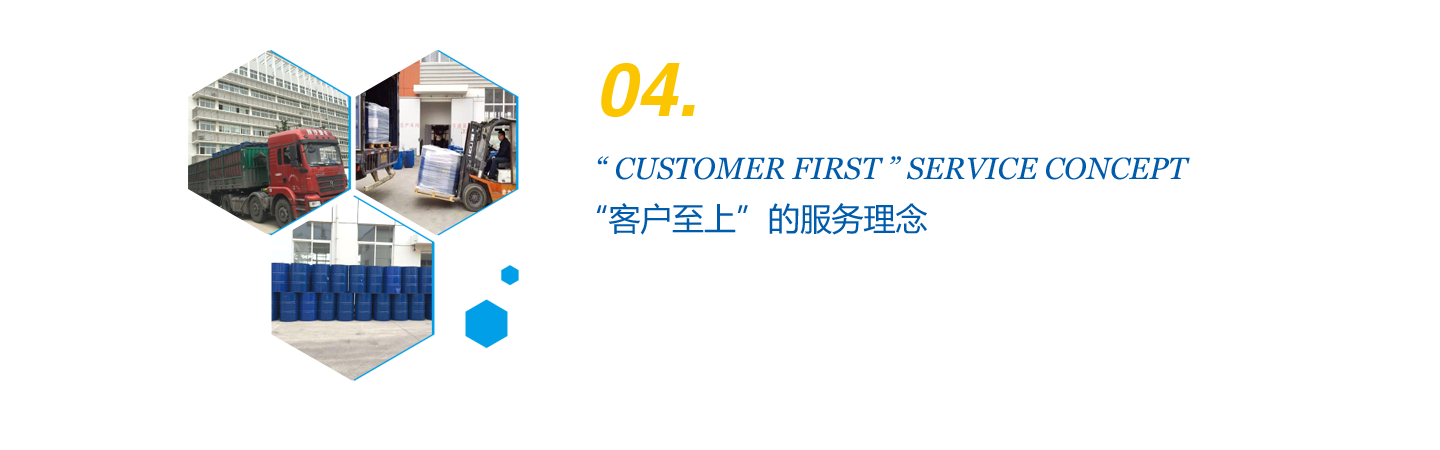
