METALWORKING CHEMICALS
-
Water-soluble quenching medium
-
Quenching oil
-
cutting fluid
-
Antirust agent
-
Metal cleaning agent
-
Water-glycol based fire-resistant hydraulic fluids
-
Welding anti-spatter
-
Pickling and passivation paste for stainless steel
-
Forging releasing agent
- Corrosion inhibitor /fogging inhibitor
-
Special lubricants
-
Water treatment agents

THI®F-528 water-based oil-like quenchant
Brand: Thinking Finechem
Model number:THI®F-528
Appearance: transparent colorless or yellowish transparent liquid
PH:9.0-11.0
package size: 25, 1000 KG / barrel
For sample and more info, please contact us (Email: info@thinkingchem.com)
Model number:THI®F-528
Appearance: transparent colorless or yellowish transparent liquid
PH:9.0-11.0
package size: 25, 1000 KG / barrel
For sample and more info, please contact us (Email: info@thinkingchem.com)

This product is a water-soluble quenchant, which can be diluted with water to different proportions. It will not produce smoke pollution during quenching. The cooling speed is slow. It can be diluted to a certain concentration (for example 15%) to have similar cooling characteristics of some fast quenching oils. This product is not likely to burn, no fire hazard, harmless to operators and the environment. It does not contain any harmful substances such as mineral oil and nitrite. It has certain functions of anti-rust, anti-corrosion, anti-foam, wetting and sterilization. It can avoid the hazard of fire and guarantee the safety of operators and equipment.

① Adjust the concentration and temperature of the solution to achieve different cooling rate between water and oil.
②No oil fume, no fire hazard, no pollution to the air or working environment.
③Can be tempered directly without cleaning. if the workpiece needs to be cleaned, it can be cleaned with water.
④overall cost-efficient.
⑤less distortion compared with PAG quenchant.
②No oil fume, no fire hazard, no pollution to the air or working environment.
③Can be tempered directly without cleaning. if the workpiece needs to be cleaned, it can be cleaned with water.
④overall cost-efficient.
⑤less distortion compared with PAG quenchant.

Subject | Indicator |
---|---|
Appearance | Colorless to yellowish transparent liquid |
Density (25℃,g/cm) | 1.05 |
pH (5%,25℃) | 9.3 |
(40℃,cst) | 600 |
Data of cooling characteristics
Concentration, % | Quenching medium temperature, ℃ | Maximum cooling speed ℃/s | Maximum cooling temperature, ℃ | V/300℃ | T600s | T400s | T200s |
---|---|---|---|---|---|---|---|
15% | 30 | 97 | 549.5 | 15 | 15.5 | 18.5 | 38.5 |

It is suitable for the quenching of high hardenability steels, such as martensitic stainless steel, tool steel, die steel, leaf springs and other large parts integral quenching.

①The concentration is determined according to the material and shape of the workpiece. The concentration is generally 10-20%, and it can be diluted with water.
② If oil is replaced by the quenchant, the system and pipes need to be thoroughly cleaned. THIF-301 metal cleaner can be used for cleaning. Quenching tank and stirring system quenching tank are mainly made by iron welding and cement casting. Because the quenchant contains anti-rust agent, it is not necessary to paint. Paint can easily react with quenching agent. The quenchant is alkaline, so copper or aluminum auxiliary facilities of the quenching tank such as pumps and pipes should be avoided as far as possible to prevent corrosion. In order to better dissipate heat and prevent the growth of bacteria, it is recommended to install a stirring device with an appropriate stirring speed.
③Pour clean water to 50% of the normal liquid level, then pour the quenchant stock solution according to the concentration ratio, and then add clean water to the normal liquid level, while stirring and circulating until the solution is well mixed.
② If oil is replaced by the quenchant, the system and pipes need to be thoroughly cleaned. THIF-301 metal cleaner can be used for cleaning. Quenching tank and stirring system quenching tank are mainly made by iron welding and cement casting. Because the quenchant contains anti-rust agent, it is not necessary to paint. Paint can easily react with quenching agent. The quenchant is alkaline, so copper or aluminum auxiliary facilities of the quenching tank such as pumps and pipes should be avoided as far as possible to prevent corrosion. In order to better dissipate heat and prevent the growth of bacteria, it is recommended to install a stirring device with an appropriate stirring speed.
③Pour clean water to 50% of the normal liquid level, then pour the quenchant stock solution according to the concentration ratio, and then add clean water to the normal liquid level, while stirring and circulating until the solution is well mixed.

1. Concentration control
Once the concentration is determined, it must remain constant so that each batch of heat-treated workpieces can remain uniform quality. The concentration detection instrument is a hand-held refractometer with a refractive index multiplication factor of 5.25. That is, the concentration of the newly prepared quenching solution = 5.25 × refractive index reading. As the quenching liquid is used for a longer time, the refractive index reading will become more and more inaccurate due to increasing amount of various impurities. the cooling curve tester need to be used to test the cooling characteristics and to determine the concentration of the quenching liquid.
2. Temperature control
Generally, quenching liquid temperature of 25-60℃ is required in production. Customers can determine the liquid temperature according to the hardenability, shape and effective size of the actual workpiece material. Within its temperature range, the higher the temperature, the slower the cooling rate. The temperature before and after quenching is controlled within a narrow range to ensure that the quenching liquid always has stable and consistent cooling characteristics, so as to obtain the best quenching effect.
Generally, the workpiece can be discharged when it cooled to the temperature of the quenching liquid. For some special materials and special-shaped parts, especially high hardenability materials, it may be necessary to discharge from the liquid at a higher temperature earlier.
3. Stirring control
Stirring can unify the temperature and concentration of the liquid at different positions of the quenching tank, so that different parts of the workpiece can obtain a more uniform cooling effect and can effectively improve the service life of the quenchant. Therefore, the quenching tank should have a good and effective stirring device and diversion device. Effective stirring can not only increase the quenching intensity, but also improve the uniformity of quenching effect. Stirring is important in improving the hardness and uniformity of quenching, controlling and reducing distortion, and make best used of the quenchant.
4. Maintenance routine of quenchant
Prevent oil stains, dust and other debris from being mixed into the quenchant and causing deterioration, stink, and further adverse effect on quenchant.
If the quenchant is in a non-use state for a long time, the quenchant should be stirred regularly (1-2 days) to prevent the growth of anaerobic bacteria and affect the effect of the quenchant. If there is bacterial growth and serious pollution, it can be treated with bactericide. The THIS-629 bactericide developed by our company is specifically aimed at the spoilage of PAG quenchant. The effect is very significant, which greatly extends the service life of the quenchant.
When intensive agitation, serious pollution, or leaks of circulation pipeline occurred, foam might be produced. If there is too much foam that affects production, you can add a defoamer.
Precipitate and filter the quenching liquid every six months to a year to keep the quenching liquid clean.
After quenching, the workpiece can be cleaned with clean water or quenching liquid. The cleaning agent can be added to the quenching tank to recycle the quenchant, which can significantly reduce the consumption of the quenchant.
When the technical requirements cannot be met by replenishing clean quenchant, it is recommended to replace the whole tank of quenchant.
Once the concentration is determined, it must remain constant so that each batch of heat-treated workpieces can remain uniform quality. The concentration detection instrument is a hand-held refractometer with a refractive index multiplication factor of 5.25. That is, the concentration of the newly prepared quenching solution = 5.25 × refractive index reading. As the quenching liquid is used for a longer time, the refractive index reading will become more and more inaccurate due to increasing amount of various impurities. the cooling curve tester need to be used to test the cooling characteristics and to determine the concentration of the quenching liquid.
2. Temperature control
Generally, quenching liquid temperature of 25-60℃ is required in production. Customers can determine the liquid temperature according to the hardenability, shape and effective size of the actual workpiece material. Within its temperature range, the higher the temperature, the slower the cooling rate. The temperature before and after quenching is controlled within a narrow range to ensure that the quenching liquid always has stable and consistent cooling characteristics, so as to obtain the best quenching effect.
Generally, the workpiece can be discharged when it cooled to the temperature of the quenching liquid. For some special materials and special-shaped parts, especially high hardenability materials, it may be necessary to discharge from the liquid at a higher temperature earlier.
3. Stirring control
Stirring can unify the temperature and concentration of the liquid at different positions of the quenching tank, so that different parts of the workpiece can obtain a more uniform cooling effect and can effectively improve the service life of the quenchant. Therefore, the quenching tank should have a good and effective stirring device and diversion device. Effective stirring can not only increase the quenching intensity, but also improve the uniformity of quenching effect. Stirring is important in improving the hardness and uniformity of quenching, controlling and reducing distortion, and make best used of the quenchant.
4. Maintenance routine of quenchant
Prevent oil stains, dust and other debris from being mixed into the quenchant and causing deterioration, stink, and further adverse effect on quenchant.
If the quenchant is in a non-use state for a long time, the quenchant should be stirred regularly (1-2 days) to prevent the growth of anaerobic bacteria and affect the effect of the quenchant. If there is bacterial growth and serious pollution, it can be treated with bactericide. The THIS-629 bactericide developed by our company is specifically aimed at the spoilage of PAG quenchant. The effect is very significant, which greatly extends the service life of the quenchant.
When intensive agitation, serious pollution, or leaks of circulation pipeline occurred, foam might be produced. If there is too much foam that affects production, you can add a defoamer.
Precipitate and filter the quenching liquid every six months to a year to keep the quenching liquid clean.
After quenching, the workpiece can be cleaned with clean water or quenching liquid. The cleaning agent can be added to the quenching tank to recycle the quenchant, which can significantly reduce the consumption of the quenchant.
When the technical requirements cannot be met by replenishing clean quenchant, it is recommended to replace the whole tank of quenchant.

25KG, 1000KG/barrel packaging. Please store in cool places. The storage life is 2 years. Transported as general chemicals.



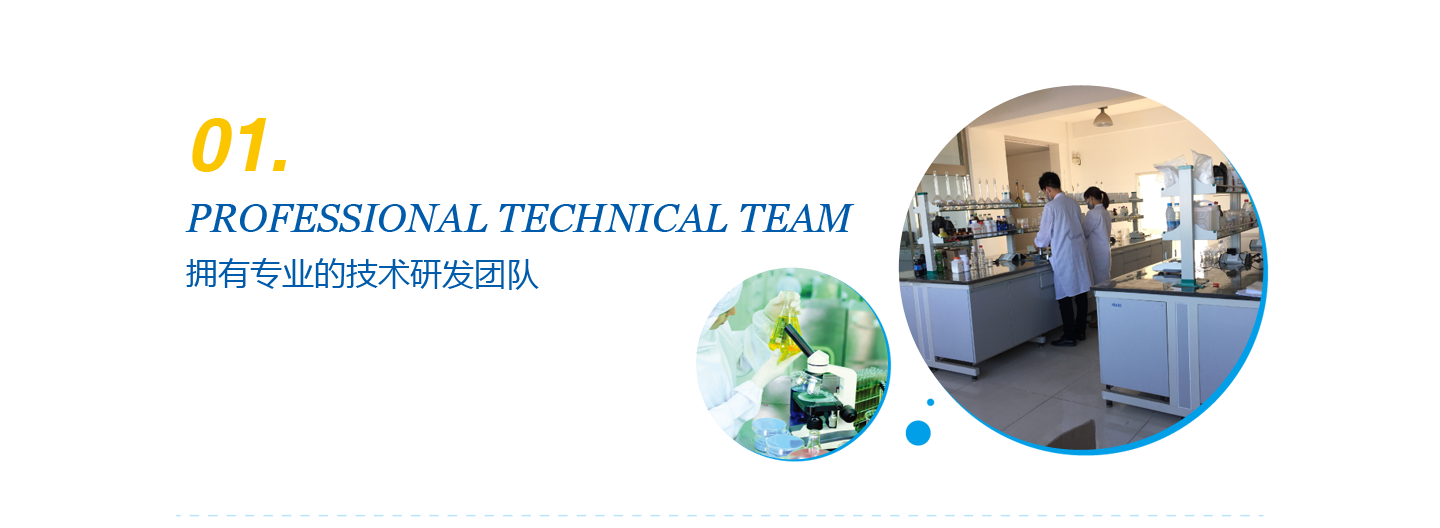
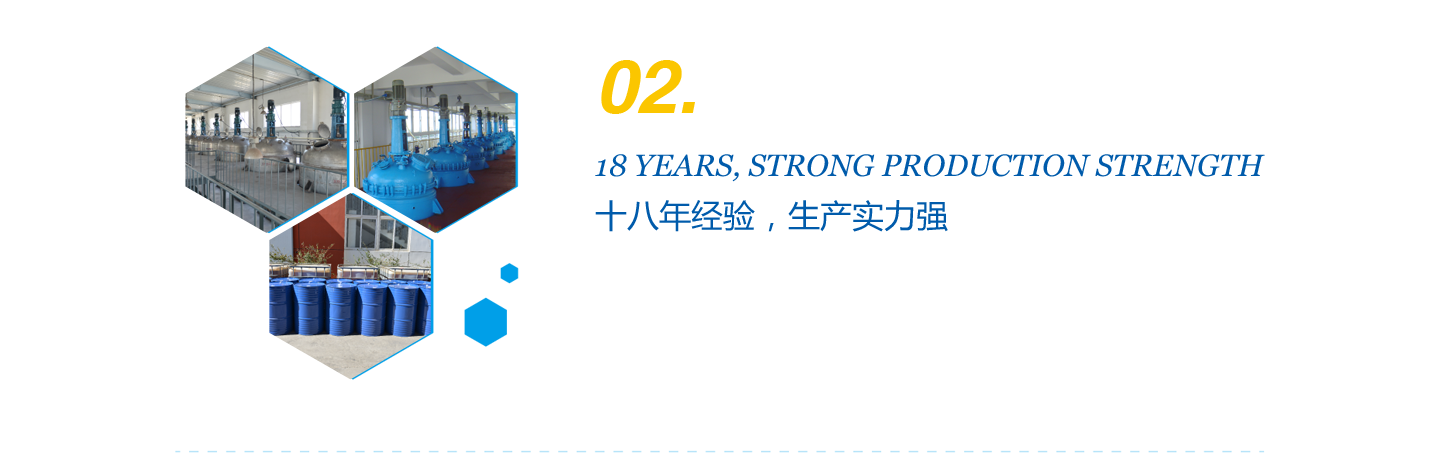
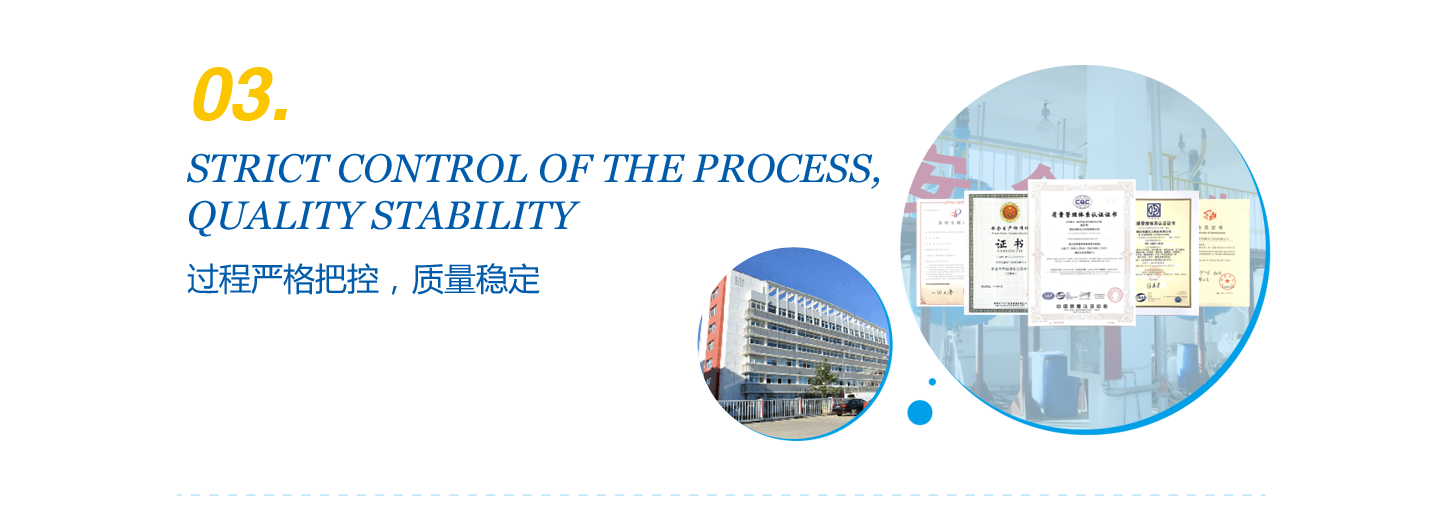
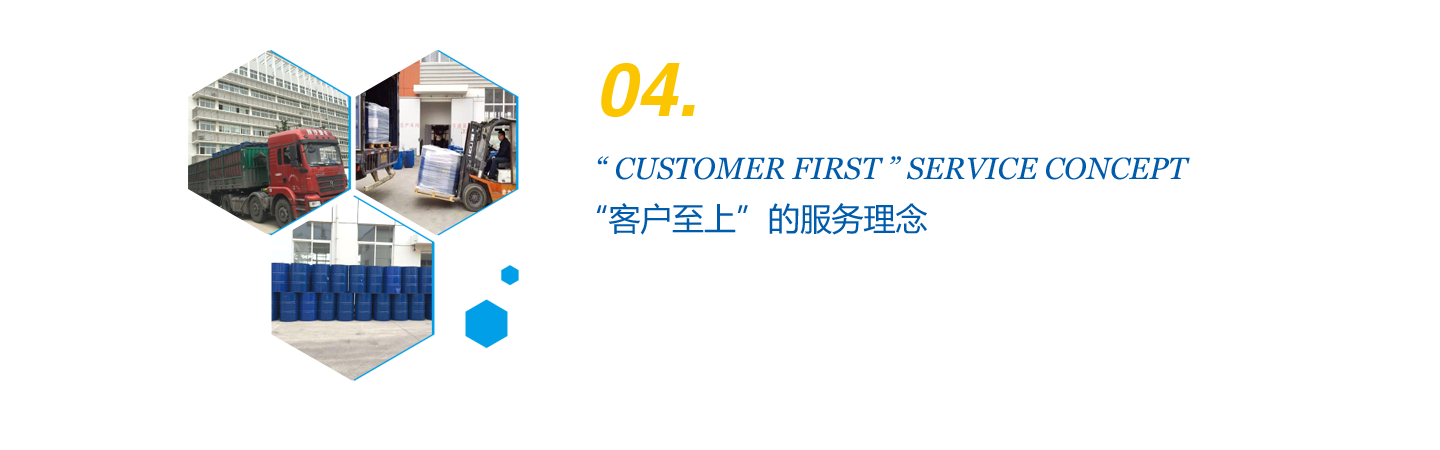
